EXCLUSIVE INTERVIEW Tesla employee shares ups and downs of working for the ‘future-building’ company
When Tesla announced the Model S almost a decade ago and started delivering the cars in 2012 few thought the world was ready for the ‘electric revolution.’ Fast-forward to 2017, Tesla is launching its third model and has plans that continue to dazzle people. But the company’s ascend has had its rough patches along the way, most recently when it came to safety issues in its main factory. One employee shares his experience working for Tesla, with all the ups and downs.
The Model 3 is hitting the market in 2017 and Tesla is far from the time when people had doubts about its cars’ success. But that doesn’t mean that all is perfect for Elon Musk’s company. Since February, when one of its employees raised questions about work safety in Tesla’s Fremont factory, the company has tackled the issue. Now another employee shared his work experience with EvoNews in an ample interview on how someone ends up working for the company, the challenges workers face every day but also why he sees his future at Tesla.
How a ‘petrolhead’ ends up building electric cars
Jonathan Galescu’s love for cars started even before he could drive one. Born in ’86 in Las Vegas, he had his first car, a VW Beetle, when he was just 14. Next, he got his hands on a ’67 Mustang fastback.
„I’ve always had the love for them, I love Mustangs. I was always playing around with them,” Jonathan says.
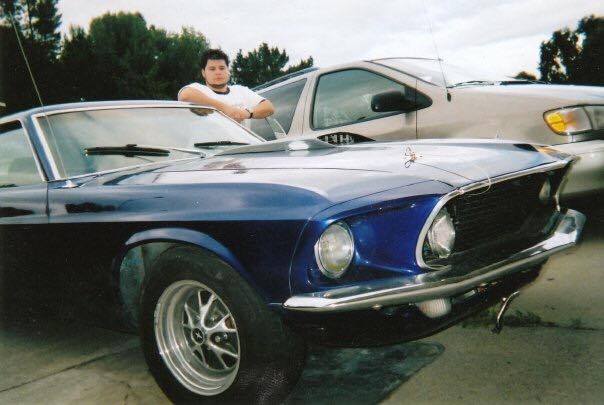
But his love wasn’t just for the brand or the looks – the 30-year-old always liked to take the cars apart and build them back together. And the skills on his resume were the ones that caught Tesla’s eye. Even if, as Jonathan admits, he wasn’t really looking for a job back then and almost hung up. It all happened three years ago:
„I just had my resume out there and they called me out of the blue. I wasn’t looking for a job, actually, I almost hung up on the lady because I wasn’t understanding what she was saying, she had a very thick English accent. I said ‘I’m about to hang up on you, I don’t know what you’re saying.’ So she adjusted her microphone and told me she works at Tesla and they’d like to see me, come out for an interview, offer me a position there. And she asked if I could come tomorrow and I said I don’t have a suit and tie and she said ‘we don’t need a suit and tie, this is business casual, just come out with a nice colour shirt and you’ll be ok.’ So I went down, took the exam to measure some bolts and put something together and I met with three people and the next week I started working at Tesla. It happened faster than I imagined.”
Not only did Jonathan not expect a job offer from Tesla, but he didn’t know what he was getting himself into, as he recalls.
„They just pretty much put me in to build the Model S frames so I was building what we called the underbody – it’s anything from building the big parts and welding. Eventually, they took my shift and took us to do prototypes for the Model X so I got to build the ‘golden cars’ of Tesla. I got to build the Model X by hand and test-crash vehicles, all kinds of stuff. Then later I became a body repair technician for the Model X where I do all the body work and repairs that are needed throughout the day,” Jonathan says.
He still works on the Model X today, even if he applied for a job on the Model 3.
‘Safety was skipped in the beginning’
As he started to work at Tesla’s factory in Fremont, California, Jonathan Galescu soon found that the ‘dream future’ where people would drive electric came at a cost – twelve hours a day, six days a week.
„Pretty much since I’ve been there I worked almost twelve hours almost everyday. There have been a few exceptions. Recently they were working us a lot. We work, we definitely work there,” the employee says.
The S-line is very labour intensive, it’s a very difficult line to work, Jonathan adds as he feels sympathy for his co-workers: „those guys work twelve hours a day mandatory.”
„I’m on the X-line so they build a brand new body-shop. And it’s way easier, there’s a lot of robots, there’s robot upside down, it’s very cool, but it’s still labour intensive. And where they put all the parts in the car that’s all done by hand. On the Model X line, we’re a five-men team and we handle repairs all day long for eight to twelve hours a day. It’s pretty repetitive, it’s not easy, it’s not hard. There are days where ‘ok, we’re not dying’ and then there are days where we’re getting beat up over there,” Jonathan says.
And that’s where work safety comes up.
Tesla’s total recordable incidence rate in 2015 was 31 percent higher than the industry-wide incident rate (8.8 injuries per 100 workers, compared to 6.7 for the automobile manufacturing industry as a whole), a Worksafe analysis shows. As for 2016, Tesla’s total injury rate for 2016 was 8.1 injuries per 100 workers. The organisation’s report, recently published, also notes that the rate of serious injuries at Tesla’s Fremont plant — those that result in days away from work, restricted duty, or job transfer — was approximately double the industry rate for 2015.
„I think safety was skipped in the beginning, there was a big pressure, demand to build these vehicles. We have a very big back order of vehicles to build and ship around the world. A lot of people younger than me have life changing injuries that will never heal right, they’re never going to be the same. I’ve seen people hurt all the time there, I’ve been personally hurt. I’ve been hit in the chest with a massive part, the rear underbody. Right now I’m recovering from an injury, I have muscle spasm in my muscle in my right shoulder just from non-stop repairs. Working eight or twelve hours a day, after 30 days it’s not if you’re going to get hurt, it’s when you’re going to get hurt,” Jonathan says.
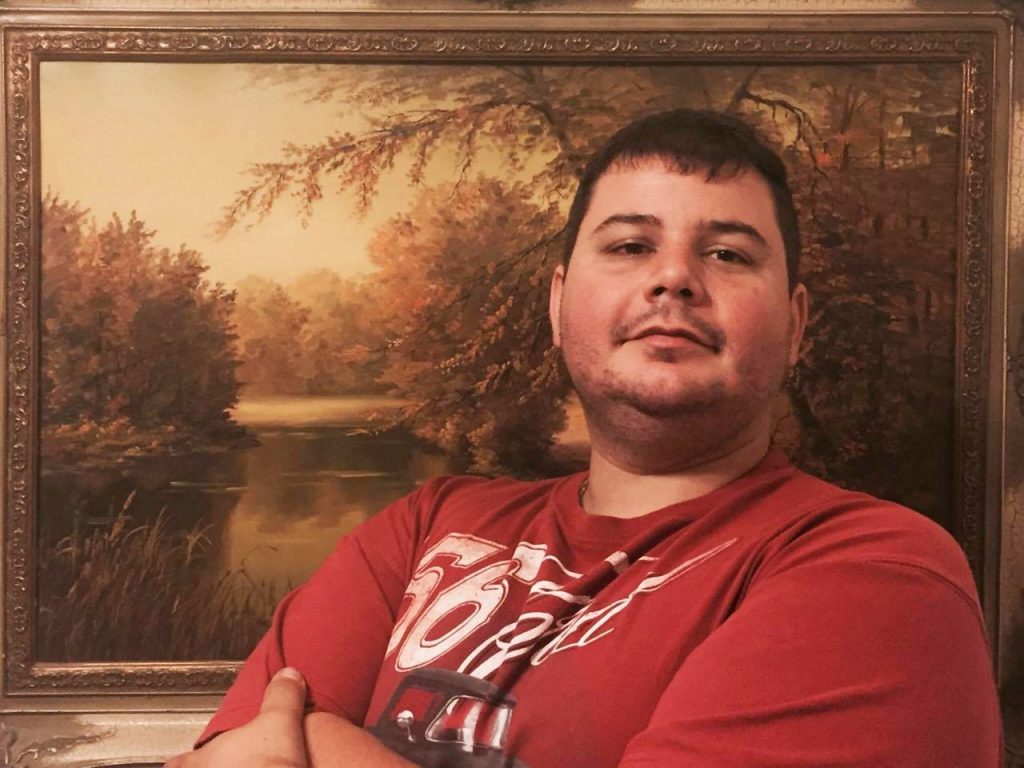
The issue came up after Jonathan and a few other co-workers stepped up and starting asking questions.
„Now it’s starting to be a number one priority, but that’s only because a few of us have started to step up and say ‘these are not safe working conditions’ and we’re trying to form a union and show that we want to make changes here. Tesla is now starting to make it safer, in my area we’re down to eight hours a day. But that’s only because we stepped up,” he says.
Tesla versus the unions
Tesla workers unsatisfied with the conditions are now working with the United Automobile Workers union in hopes to change things around the factory. And it has pushed the company to take steps forward in matters regarding work safety.
„Things are starting to change, they’re really pushing on safety, Tesla’s having a better attitude about it and it’s unfortunate that it took so many people to get hurt and it took us to speak up and tell them ‘hey, this is not right!’ Yes, we can have a safer factory, but there’s a lot of work to be done,” Jonathan thinks.
Dealing with the pressure, Tesla recently announced its goal is to ‘have the safest factory in the auto industry.’ Accusing the UAW of a concerted and professional media push intended to raise questions about safety at Tesla, the company released numbers regarding the improvements in the past year. Not before admitting it did not manage the issue perfectly in the past.
„As we look at our safety record in prior years, we realize that we have not been perfect. No car factory is perfect but particularly given that Model S and X were the first cars we built at more than tiny volumes, we fully acknowledge that they were not designed for ease of manufacturing – far from it. As would be expected, we have since learned many lessons, including how to improve the production process for the well-being of our colleagues.
The third shift, ergonomic improvements and increased safety awareness have collectively led to a 52% reduction in lost time incidents and a 30% reduction in recordable incidents from the first quarter of 2016 to the first quarter of 2017. In addition, through the end of Q1 2017, the factory’s total recordable incident rate (TRIR), the leading metric for workplace safety, is 4.6, which is 32% better than the industry average of 6.7. This data shows that there has been a dramatic improvement in employee safety, we are now significantly better than industry-average, and we continue to improve each day,” the Tesla team said in a blog post.
“Our goal is to have as close to zero injuries as humanly possible and to become the safest factory in the auto industry,” they added.
The ambitious goal set by Tesla isn’t stopping some of the employees from trying to form a union and fighting for better working conditions and wages.
„Tesla tried to do some anti-union campaigning, saying the union dues are going to be expensive. We want to make it fair, we want to bring Tesla down to our level and have safer working conditions, better wages. The union effort is very strong, we have a big movement going on right now. A guy came up to me in the beginning and told me I’m like a magnet, where I either drew people to me, people who wanted to learn about it, or drew people away, because they were scared. But now people around the factory are shaking my hand and saying ‘thank you’ for having a voice for them. It just took a few individuals to say ‘look, this is not right, we can’t continue to work like this,’” Jonathan says.
He added that, despite the media coverage and reactions, he wouldn’t call the issue a ‘scandal.’
Also, the Tesla employee doubts Elon Musk ‘really knew what was going on one hundred percent of the time,’ as Musk has other projects too.
On Elon Musk, clean energy and the future
Jonathan Galescu has been working at Tesla for the past three years and is a production technician but says he never personally met Elon Musk, the company’s CEO. He would like to, as he says he heard stories of his personal involvement in building the cars.
„I’m not sure if this is true, but I heard he would come down at the line and build one part at a time so he could say he built one car a year. Elon does come down, he gives speeches in certain areas sometimes, I’ve seen him walk through the factory a few times, I’ve seen him ride his bicycle a few times. I never got to sit and talk to him personally or shake his hand, I would like to meet him one day,” Jonathan says.
He shows appreciation for what Elon Musk is trying to build and is on board for a clean energy future.
„Elon is building a better future. We do need to go to clean energy. Elon came up with this and put up the money and wanted to start this company, bringing jobs back to America, especially in the San Francisco Bay Area, where jobs like these are almost non-existent. We’re not building a gas-powered vehicle, we’re building clean energy and as our planet is worse pollution wise we need to go to cleaner energy. People are starting to realise that. I think eventually there’ll be only electric cars, solar cars. I think Tesla is going to strive. We have orders and I think it’s just going to grow. Tesla didn’t just build another car, they rethought the car,” Jonathan says.
Even if admittedly it’s not the kind of car he fell in love with at a young age:
„The love of a car is the love of a car. There’s nothing to me better sounding than a big throbbing V8 engine, but the way the Model S looks, it’s such a beautiful, elegant car. I did do body work on that as well and I fell so honoured to do this kind of work. I’m literally like Henry Ford when he started the assembly line. Now I’m working at Tesla building the future of electric cars. I’m just happy to be part of history.”
And maybe the Galescu name will also be part of the future, as Jonathan says he’d like to retire from Tesla and even have his kids come work for the company.
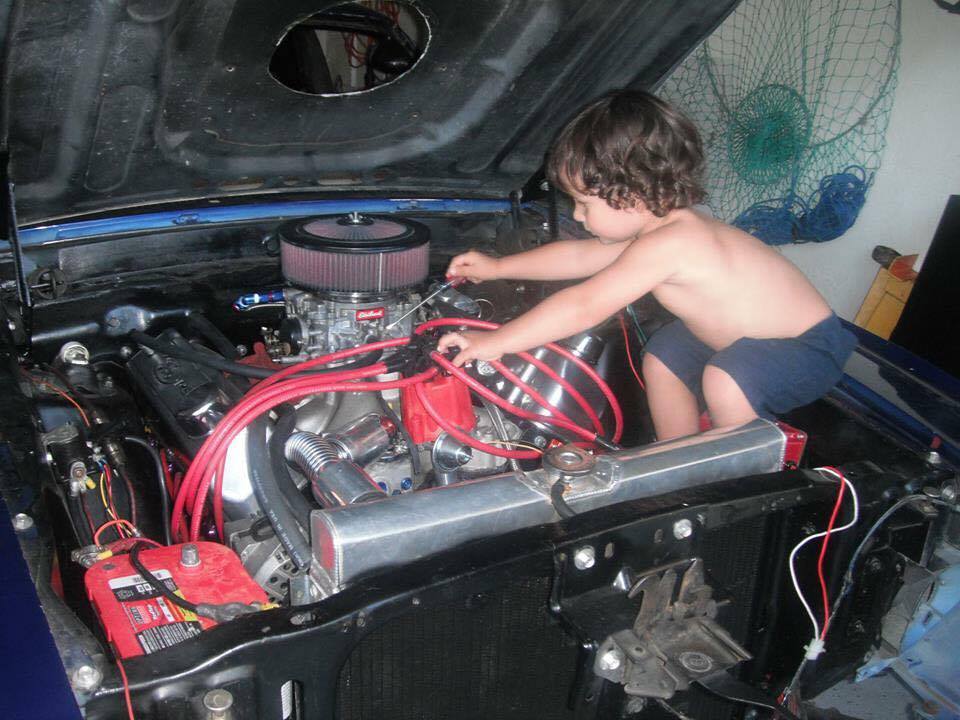